products categories
- Battery Production Equipment Line
- Battery Lab Pilot Equipment Line
- Lithium Battery Pack Assembly Line
- Solid State Battery Assembly Line
- Sodium Ion Battery Production Line
- Supercapacitor Assembly Line
- Lithium Ion Battery Recycling Plant
- Dry Electrode Preparation Solution
- Perovskite Based Solar Cell Lab Line
- Li ion Battery Materials
- Cathode Active Materials
- Anode Active Materials
- Customized Battery Electrode
- Coin Cell Parts
- Lithium Chip
- Cylindrical Cell Parts
- Battery Current Collectors
- Battery Conductive Materials
- Electrolyte
- Metal Mesh
- Battery Binder
- Separator and Tape
- Aluminum Laminate Film
- Nickel Strip
- Battery Tabs
- Graphene Materials
- Nickel Felt
- Titanium Fiber Felt
- Battery
- Battery Pack Machine & Compoments
- Battery Pack Compoments
- Turnkey Solutions Battery Pack Assembly Line
- Cell Sorter
- Battery Pack Spot Welder
- Laser Welder
- Battery Charging Discharging Tester
- Battery Pack Aging Machine
- Battery Pack Comprehensive Tester
- CCD Visual Inspector
- Battery Pape Sticking Machine
- BMS Testing Machine
- Al Wire Bonding Machine
- Lithium Battery Machine
- Battery Tester & Analyzer
- Battery Safety Tester
- Battery Material Tester
- Rolling Press Machine
- Spot Welding Machine
- Vacuum Mixer Machine
- Crimping/Disassembling Machine
- Vacuum Sealing Machine
- Electrolyte Filling
- Stacking/Winding Machine
- Electrode Cutter/Slitter
- Pouch Forming Machine
- NMP Solvent Treatment System
- Lithium Battery Production Plant
- Vacuum Glove Box
- Furnaces
- Coaters
- Hydraulic Press
- Ball Mill
- Planetary Centrifugal Mixer
- Cutting Machine
- Laboratory Machine
- Metal Foam
contact us
- If you have questions, please contact us, all questions will be answered
- WhatsApp : +86 13174506016
- Email : David@tmaxcn.com
- Email : Davidtmaxcn@gmail.com
- Add : No. 39, Xinchang Road, Xinyang, Haicang Dist., Xiamen, Fujian, China (Mainland)
Automatic Battery Separator Slitter Machine For Thin Film/Foil Slitting With Roll to Roll System
Model Number:
TMAX-RP600Compliance:
CE CertifiedWarranty:
One year limited warranty and lifetime supportPayment:
L/C D/A D/P T/T Western UnionDelivery Time:
5 days
- WhatsApp : +86 13174506016
- Email : David@tmaxcn.com
- Email : Davidtmaxcn@gmail.com
- Wechat : 18659217588
Previous:
Automatic Battery Electrode Slitter Machine For Cathode/Anode Sheet CuttingNext:
Automatic Film Copper/Aluminum Foil Laminating With Slitting Machine
Automatic Battery Separator Slitter Machine For Thin Film/Foil Slitting With Roll to Roll System
Introduction
This equipment is mainly used for separator slitting and rewinding. After the transmission mechanism and the slitting mechanism, the required slitting and rewinding of the fixed width separator are realized, and the winding process is completed.
Installation requirement
- Ambient temperature: 5 ~ 40℃;
- Relative humidity: 20 ~ 50%;
- Working environment: indoor, should ensure that the site air dry and smooth (no water and no oil)
- Altitude: Less than 1000 meters.
- Power supply: 3-phase 5-wire 380V, 50HZ, voltage fluctuation range: +8% ~ -8%; Total power 11kW;
- Compressed air: after drying, filtering and pressure regulation: the outlet pressure is greater than 0.5MPa;
Basic specification
No |
Item |
Technical parameters |
Note |
1 |
Applicable substrate |
PP/PE lithium-ion batteries separator |
|
2 |
Substrate thickness |
5-30 um |
|
3 |
Applicable substrate width |
200-550 mm |
Roller surface width 600 mm |
4 |
Slitting width |
50-500 mm |
Depends on the material |
5 |
Unwinding diameter |
Dia400 mm |
|
6 |
Winding system |
Surface center winding |
|
7 |
Unwinding system |
Active constant tension release system |
|
8 |
Slitter system |
Knife suspended front cut |
|
9 |
speed |
Knife suspended front cut Mechanical speed 200m/min |
Depends on the material |
10 |
Slitting width accuracy |
0.2mm |
|
11 |
Control mode |
PLC+ touch screen |
|
12 |
Width of waste edge slitting |
>15 mm |
Unwinding specification
No |
Item |
Technical parameters |
Note |
1 |
Tension control system |
With the motor and tension sensor to form a closed loop, constant tension winding, Unwinding tension 8N Min.-60N Max./±1N |
|
2 |
Correction mode |
Automatic EPC control, stroke 140mm, with automatic left and right displacement function: with automatic micro-pendulum function |
|
3 |
Slight swing speed |
6-100m/min |
|
4 |
Slight swing stroke |
Micro-pendulum and deviation correction are not used at the same time: micro-pendulum stroke ±25mm When the micro pendulum and correction are used at the same time: the micro pendulum stroke is ±3mm |
|
5 |
Unwinding correction accuracy |
±0.2 mm |
|
6 |
Winding method |
Use 3/6 inch shaftless inflatable chuck to tighten; Roll can be simultaneously Implement volume up and volume down. |
|
7 |
Maximum winding diameter |
Maximum diameter of winding roller: dia400 mm |
|
8 |
Maximum bearing capacity of the inflatable shaft |
100kg |
Winding specification
No |
Item |
Technical parameters |
Note |
1 |
Winding arm |
3 inch plate inflatable shaft winding |
|
2 |
Winding adjustment device |
Adopt cylinder pressure or buffer, adjust the air pressure of the winding arm according to needs, and the winding side is neat. |
|
3 |
Driving roll |
High precision polyurethane rubber roller, the hardness of Shore 65~70 degrees |
|
4 |
Winding power |
Surface center winding |
|
5 |
Tension control |
The winding tension is controlled by servo motor |
|
6 |
Maximum winding diameter |
φ330 mm |
|
7 |
Static eliminator |
Ion-air electrostatic eliminator eliminates diaphragm static electricity |
|
8 |
Edge closing mechanism |
Side winding mechanism (two sets of independent arms) Minimum width of side material: 15-25mm; Coil diameter of side material: maximum coil diameter 200mm when the width of side material is 15-25mm; The maximum roll diameter is 330mm when the width of the side material is 25-100mm; |
Machine Configuration Table
Electrical parts
No |
Item |
Technical parameters |
Note |
1 |
Man-machine interface |
10 inch Wiren touch screen (1) |
|
2 |
PLC |
Mitsubishi /LS(1) |
|
3 |
Unwinding servo motor (1 set) Traction servo motor (1 set) Winding servo motor (2 sets) |
Wacoda /LS(4 sets) |
|
4 |
Correction system actuator |
Bianfu (1 set) |
|
5 |
Tension sensor |
Hongrui/Puliyuan (2) |
|
6 |
Static eliminator |
Xinpu /kapper(1 set) |
|
Machine’s specification
No |
Item |
Technical parameters |
Note |
1 |
Winding arm |
2 sets (including two 3-inch inflatable shafts) |
|
2 |
Cut components with a straight knife |
A set |
|
3 |
Side material independent arm |
Two sets |
|
4 |
Unwinding clamp head |
3/6 inch share (1 set) |
|
5 |
Active winding rubber roller |
1 piece (material, imported polyurethane, Shore hardness 65-70 degrees) |
|
6 |
Active pull aluminum roller |
4 (Material, Aluminum 6063, hardened anode, |
|
7 |
Edge material winding rubber roller |
1 piece (material, imported polyurethane, Shore hardness 65-70 degrees) |
|
8 |
Passive aluminum roller |
7 (Aluminum 6063, hardened anode) |
|
9 |
Flattening roller |
Curved roll (1 piece) |
|
10 |
Pneumatic element |
Artac /SMC |
|
11 |
Rolling element |
Japan NSK/NTN, E-class bearing |
|
Accessories
No |
Name |
Specification |
Quantity |
Note |
1 |
Cutter weight |
50/20/10/5/2/1/0.5/0.2 mm |
10 pcs each unit |
|
2 |
Crimping roller |
30mm |
1 pcs |
|
3 |
Open end wrench |
8-piece set |
1 set |
|
4 |
Toolbox |
345*155*155mm iron toolbox |
1 pcs |
|
5 |
Hex wrench |
9-piece set |
1 set |
|
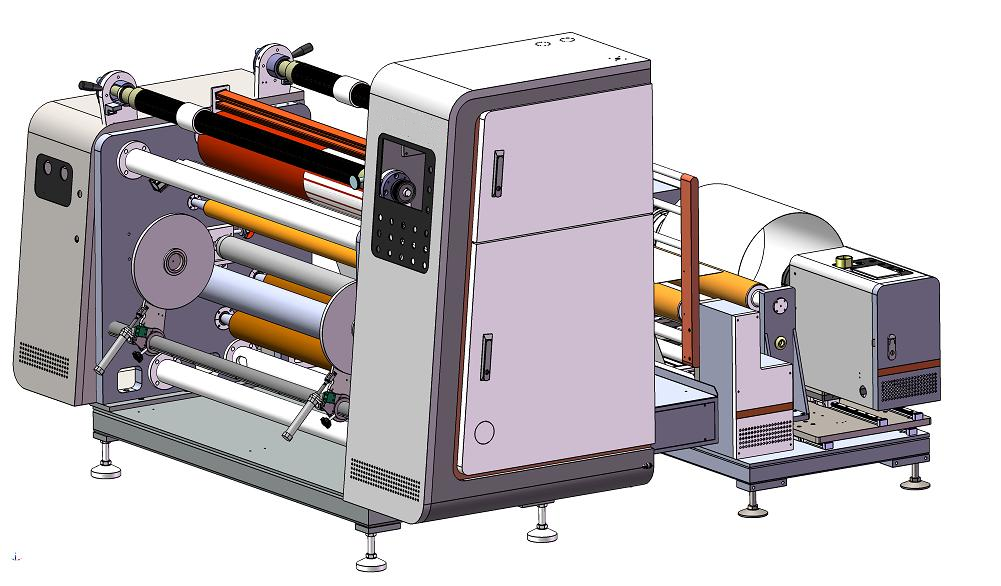