products categories
- Battery Production Equipment Line
- Battery Lab Pilot Equipment Line
- Lithium Battery Pack Assembly Line
- Solid State Battery Assembly Line
- Sodium Ion Battery Production Line
- Supercapacitor Assembly Line
- Lithium Ion Battery Recycling Plant
- Dry Electrode Preparation Solution
- Perovskite Based Solar Cell Lab Line
- Li ion Battery Materials
- Cathode Active Materials
- Anode Active Materials
- Customized Battery Electrode
- Coin Cell Parts
- Lithium Chip
- Cylindrical Cell Parts
- Battery Current Collectors
- Battery Conductive Materials
- Electrolyte
- Metal Mesh
- Battery Binder
- Separator and Tape
- Aluminum Laminate Film
- Nickel Strip
- Battery Tabs
- Graphene Materials
- Nickel Felt
- Titanium Fiber Felt
- Battery
- Battery Pack Machine & Compoments
- Battery Pack Compoments
- Turnkey Solutions Battery Pack Assembly Line
- Cell Sorter
- Battery Pack Spot Welder
- Laser Welder
- Battery Charging Discharging Tester
- Battery Pack Aging Machine
- Battery Pack Comprehensive Tester
- CCD Visual Inspector
- Battery Pape Sticking Machine
- BMS Testing Machine
- Al Wire Bonding Machine
- Lithium Battery Machine
- Battery Tester & Analyzer
- Battery Safety Tester
- Battery Material Tester
- Rolling Press Machine
- Spot Welding Machine
- Vacuum Mixer Machine
- Crimping/Disassembling Machine
- Vacuum Sealing Machine
- Electrolyte Filling
- Stacking/Winding Machine
- Electrode Cutter/Slitter
- Pouch Forming Machine
- NMP Solvent Treatment System
- Lithium Battery Production Plant
- Vacuum Glove Box
- Furnaces
- Coaters
- Hydraulic Press
- Ball Mill
- Planetary Centrifugal Mixer
- Cutting Machine
- Laboratory Machine
- Metal Foam
contact us
- If you have questions, please contact us, all questions will be answered
- WhatsApp : +86 13174506016
- Email : David@tmaxcn.com
- Email : Davidtmaxcn@gmail.com
- Add : No. 39, Xinchang Road, Xinyang, Haicang Dist., Xiamen, Fujian, China (Mainland)
1.2 Tons Environmental Protection And Recycling Machine Recycling Equipment Production Plant For Retired Lithium Battery
Model Number:
TMAX-1200Type:
AutomaticCompliance:
CE CertifiedWarranty:
One year limited with lifetime supportMOQ:
1Payment:
L/C D/A D/P T/T Western UnionDelivery Time:
5 days
- WhatsApp : +86 13174506016
- Email : David@tmaxcn.com
- Email : Davidtmaxcn@gmail.com
- Wechat : 18659217588
Previous:
PCB Circuit Boards Computer Boards Recovery Plant Scrap Recycling Machine Electronics Waste E-Waste Recycling EquipmentNext:
300KG Waste Lithium Battery Recycling Equipment Li Ion Battery Recycling Production Plant
1.2 Tons Environmental Protection And Recycling Machine Recycling Equipment Production Plant For Retired Lithium Battery
Introduction
1.Overview: This production line is a green and efficient recycling production line for waste lithium batteries, with the function of integrating coarse crushing, pyrolysis, cooling, fine crushing, grinding, screening, dust collection, smoke collection, etc., continuous and environmentally friendly integrated equipment, after processing by recycling equipment to get:
1. Nickel-cobalt-manganese mixed powder for positive electrode material
2. Graphite powder for negative electrode material
3. Copper powder
4. Aluminum powder
5. Stainless steel and steel shell
6. Plastic and other organic debris
2. Raw Materials: suitable for all kinds of new energy waste car power animal batteries, two-wheelers batteries, solar energy storage battery, subway high speed railway emergency battery, laptop cell phone Bluetooth rechargeable 3C electronic product battery, drone battery, balance car battery, communication emergency battery, coal mine energy storage battery and other fields, lithium iron phosphate, lithium ternary, lithium manganate, lithium cobaltate, etc. can be universal.
Raw Material
The lithium battery recycling production line is used for dismantling andrecycling the Soft pack-age battery, cellphone battery,Shell battery,Cylindrical battery etc. Different types of lithium batteries have different recycling procedures.
*Production line 1 ton / hour footprint: length 56 m * width 10 m * height 6 m
*Production line operation mode: continuous production
*Production line operation direction: left or right (determined by the user's workshop layout)
*Total power of production line: 1 ton/hour 238KW, voltage 380V/50HZ
Final Products
Graphite Powder
Cobalt Acid Lithium Powder
Copper
Aluminum
Technological Process
The entire production line of lithium battery recovery equipment is fed by conveyor materials into the crusher of the first process for coarse crushing. The coarse crushed materials are fed by conveyor to the secondary crusher for secondary crushing. The crushed materials from the secondary crusher enter the conveyor and magnetic separation equipment is installed to separate the iron in the materials. After the iron is removed by the material conveyor and magnetic separator, it enters the three crusher for fine crushing, crushing the material to powder. Materials in powder state enter the cyclone separator through the negative pressure system for air filtration, and then fall onto the air flow separator through the fan. The air flow separator separates materials of different densities to obtain metal separation, while all non-metals are brought into the pulse dust collector through the negative pressure system for concentration. The filtered tail gas will continue to be sent by the negative pressure system to the tail gas treatment equipment for air purification, so that it meets the national emission standards before being discharged at high altitude.
Shredder: Shredded lithium batteries into smaller pieces.
Hammer crusher: For the secondary crushing of shredded materials.
Grinder: For the grinding of the crushed materials.
Separation machine: Separate the materials after being ground.
Collector: Collect and release the dust .
Pulse purifier (air cleaner): Clean all the dust produced during the operation of the wholesystem.
Classifying screen:Screen the materials sorted by the separation machine,and screen out oflarger metal materials.
Magnetic machine: Separate nickel from the metals.
Gravity separator:Separate those finer materials got from the screening machine and separatethe metal completely.
High-pressure blower: Keep the whole system in a negative state so as to collect the materialsand purity the air.
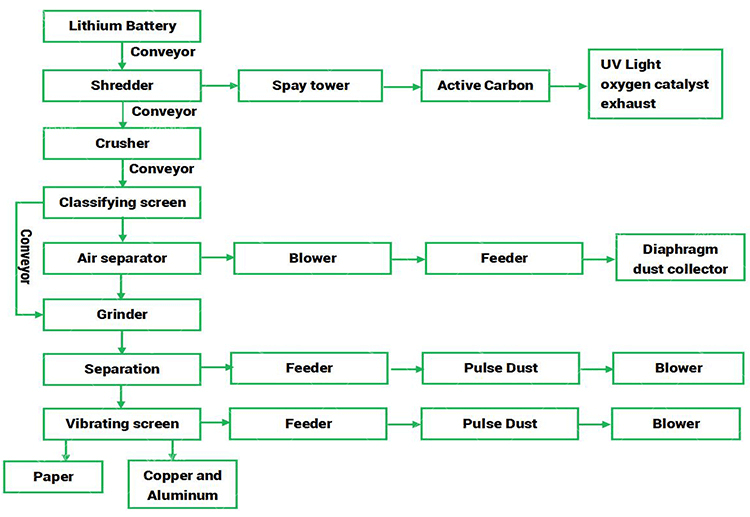
Introduction to the configuration of each unit of equipment
Front-end Shredding+calciner equipment
NO. |
Equipment name |
Power parameter |
Quantity |
Remarks |
1 |
One-stage shredding conveyor |
1.Power 3KW 2.Width 600mm 3.PVC canvas belt 4.Chain link drive 5.Length 10 meters |
1Set
|
TMAX |
2 |
One-stage twin-shaft shredder |
1.Power 30KW 2. Number of blades 30 pieces 3.Blade material hard alloy SKD11 forging 4.Case thickness 20mm |
1Set
|
|
3 |
High-temperature calcining furnace |
1.High temperature refractory brick inner liner diameter 1.25m 2. Heavy oil combustion assisted heating 3.Cylinderdiameter1500mm*length 12m 4. Reducer drive, speed adjustable 5. Power 15KW |
1Set
|
TMAX |
4 |
Shredder Base support frame |
1. Height 3.5 m 2.Length 3800*2800mm 3. 160mm heavy channel steel welded 4. Platform to build fence type guardrail, climbing ladder 5. The first and last end of the extraction hole is installed with manual air regulating valve 6. High temperature glass window installed at the end |
1Set
|
TMAX
|
5 |
Calcining furnacebody Platform support |
1. Height 1.5 m 2.Length 12.5 m width 1.8 m 3.Welded with heavy duty 180 square steel 4.Separate support for import and export |
1Set
|
TMAX |
6 |
Cooling furnace platform support frame |
1.height 1m 2.length 9m width 1.5 m 3.Made of heavy duty 180 square steelwelded 4.Separate support for import and export |
1Set
|
TMAX |
7 |
Low temperature cooling furnace |
1. Cylinder diameter 1200mm * 8m length 2. 2 inch water outlet valve 3. Water tank volume 6 cubic meters 4. Reducer drive, speed adjustable 5. Power 5.5KW |
1Set
|
TMAX
|
8
|
High temperature exhaust gas purification spray tower |
1. Tower diameter 1500mm *4500mm height 2. Material stainless steel 201 3. Water pump power 1.5KW 4. Three layers of filters |
1Set
|
|
9 |
Low temperature exhaust gas purification spray tower |
1. Tower diameter 1500mm*4500mm height 2. Material PP 3. Pump power 1.5KW 4. Three layers of filters |
1Set
|
|
10 |
Exhaust gas activated carbon adsorption box |
1. Carbon steel anti-corrosion material 2. 300 cubes of coconut shell carbon 3. Drawer type structure |
1Set
|
|
11 |
Exhaust gas high pressure blower |
1. Power 15KW 2. Air volume 18000 cubic meters 3. Motor direct connection drive |
1Set
|
|
12 |
Exhaust ventilation duct |
1. Duct diameter 500mm 2. Carbon steel material 3. Carbon steel material at the front, galvanized spiral duct at the back |
Matching 30m |
Luoyang Lituo |
13 |
Control electric cabinet |
1. using Chint electrical appliances 2. Explosion-proof electric cabinet 3. Fault warning sound control 4. Camera monitoring |
1Set
|
|
Back-end crushing + screening equipment
|
||||
1 |
Lithium battery crusher |
1.Heavy duty thickened shell thickness 16mm 2.Model 800 rotating diameter 700mm 3.Power 30KW national standard pure copper wire motor 4.50 pieces of knife plate 5.frame using 120mm large channel steel 6.The upper box cover quick disassembly structure 7.Screen aperture 14mm |
1Set
|
|
2 |
Lithium battery grinding machine |
1.Model 750 rotating diameter 820mm 2.Power 37KW national standard pure copper wire motor 3.Blades are made of wear-resistant white steel 4.Double-layer circulating water coolingstructure of the body 5.Three rows of knife rollers + 1 row of impellers |
1Set
|
|
3 |
Crusher Conveyor |
1.width 600-800MM length 10m 2.PVC baffle belt 3 baffles per meter 3.motor power 3KW, cycloid gear reducer, chain drive 4.top and bottom cover fully sealed structure |
1Set
|
|
4 |
Air flow conveyor |
1.Diameter of pipe 110mm 2.Fan power 5.5KW 3. Electric discharge valve at the bottom of cone drum 0.75KW 4.conveying height 4m |
1Set
|
|
5 |
Diaphragm vibrating sieve |
1. Single layer structure 2. Sieve mesh movable screen 3. Upper and lower box fully sealed 4. Power 1.5KW |
1Set
|
|
6 |
Vibrating screen, Diaphragm Conveyor |
1.Width 600-800MM Length 10m 2.PVC baffle belt 3 baffles per meter 3.motor power 1.1KW, cycloid reducer, chain drive 4.top and bottom cover fully sealed structure |
2Sets
|
|
7 |
Grinding conveyor |
1.Width 600-800MM Length 4m 2.PVC baffle belt 3 baffles per meter 3.Motor power 1.1KW, cycloid reducer, chain drive 4.Top and bottom cover fully sealed structure |
1Set
|
|
8 |
Magnetic separation belt conveyor |
1.Width 600-800MM Length 3m 2.PVC baffle belt 3 baffles per meter 3. Motor power 0.75KW, cycloid reducer, chain drive 4.Fully sealed structure of top and bottom cover |
1Set
|
|
9 |
Mill discharge airflow conveyor |
1. Duct diameter 160mm 2.Fan 7.5KW 3.Electric discharge valve at the bottom of conical drum 2.2KW 4.conveying height 4m |
1Set
|
|
10 |
Cooling water bucket, water pump |
1. Water pump power 0.5KW 2. Water tank 1 cubic meter |
1Set
|
|
11 |
Front end 4m vibrating screen |
1.Single layer structure 2. Sieve mesh movable screen 3. Upper and lower box fully sealed 4. Power 1.5KW |
1Set
|
|
13
|
Air flow conveyor * Tail material into linear screen |
1.Pipeline diameter 110mm 2.Electric discharge valve at the bottom of cone drum 0.75KW 3.Fan power 4KW |
1Set
|
|
14 |
Air flow conveyor *to specific gravity machine |
1.Pipe diameter 110mm 2.Bucket box receiving material 3. Electric discharge valve at the bottom of cone bucket 0.75KW 4.conveying height 2.5m |
1Set
|
|
15 |
The large cyclone separatoris located in themiddle of the pulse dust collector |
1. Electric discharge valve is installed at the discharge port 2.Motor power 1.5KW 3. Discharge valve 7 liters |
1Set
|
|
16 |
Specific gravity copper and aluminumsorting machine |
1. Power 6KW 2. Vibration speed variable frequency adjustable 3. Sorting net 800 X 1350mm 4. Blower and vibration frequency frequency adjustment |
1Set
|
|
17 |
Large pulse dust collector |
1.240 bags of polyester heat-resistant needle-punched felt areused for dust bags 2.5 pulse control valves 3.Pulse controller digital module 4.8KG air pressure for air compressor 5.Sealed with upper and lower Box links 6.Air inlet hole on the side of the upper box and air extraction hole on the side 7.fan power 18.5KW |
1Set
|
|
18 |
Pulsed dust collector for copperand aluminum |
1.96 bags of polyester heat-resistant needle-punched felt are used for the dust bag. 2.8 pulse control valves 3.Pulse controller digital module 4.Using the upper and lower box link seal 5.The lower box open air inlet hole 6.Power 5.5KW |
1Set
|
|
19 |
Vibrating sorting screen |
1.Length 3m width 800mm 2.Double vibration motor power 0 .75KW*2 3.Divided into two outlets, screen 100 mesh 4.Add dust collection hood 5.Outlet distance from the ground 1300mm |
1Set
|
|
20
|
Magnetic roller magnetic separator |
1.Power 1.1kw 2.Chain drive 3. Magnetic block 6000 gauss 4.Automatic iron unloading mechanism added |
1Set
|
|
21 |
Horizontal conveyor magnet machine below |
1.Width 600MM Length 4m 2.Motor power 0.75KW , cycloidal needle reducer 3.Chain drive 4.magnetic gauss drum magnet 7000 |
1Set
|
|
22 |
Rear end hexagonaldrum screen |
1. hexagonal drum structure 2. 24 movable screens 3. Upper and lower box fully sealed 4. Power 5.5KW |
1Set
|
|
23 |
Dust removal duct |
1.Diameter 600/500/400mm\300mm\ 200mm 2.Elbow, flange, flange plate, tee, reducer, etc. 3.Length about 80m 4.Pipeline configuration pulse automatic cleaning structure |
1Set
|
Luoyang Lituo |
24 |
Control electric cabinet |
1.Automatic flip function 2.Overload protection device 3.voltmeter, ammeter 4.Emergency stop switch 5.Sound and light alarm function |
3Sets
|
|
25 |
Copper and aluminum selectionCircular Vibrating Sieve |
1.Stainless steel screen 2.Diameter 400mm 3.Sieve double layer |
1Set
|
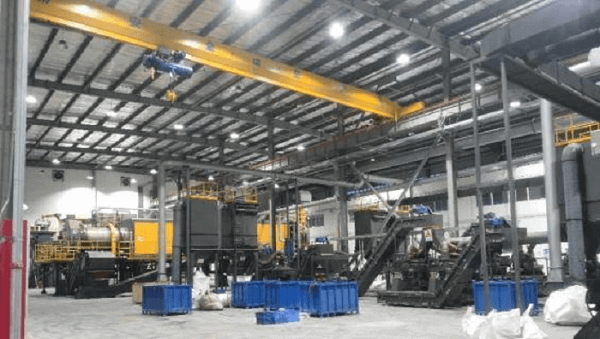
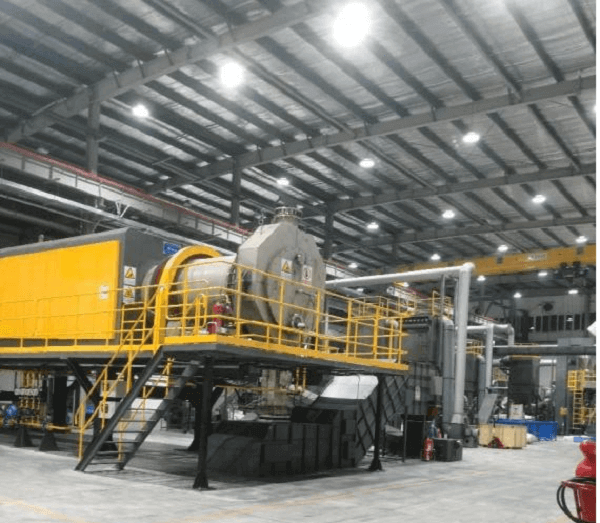
Our Certifications
Cooperative Brand